Drying of honeycomb ceramic
Our client, one of the leading manufacturers of honeycomb ceramics for catalytic converters had drying issues leading to significant production reject rate.
Former process
Our customer is one of the leading honeycomb ceramic producers for catalytic converters. During the process, a drying operation must be carried out between the extrusion and the firing of the ceramic.
The conventional hot air drying solution used previously led to significant production scrap, up to 20%, due to internal tensions in the ceramic part, created by heterogeneous drying. Moreover, the drying process took several hours, which was not compatible with flexible production.
Customer needs
Drying of honeycomb ceramic must be fast, perfectly repeatable and uniform in order to prevent internal constraints leading to rifts and significant scrap rates.
The extrusion stage must be performed at a humidity rate of 40% while firing must be carried out at a humidity rate under 2%.
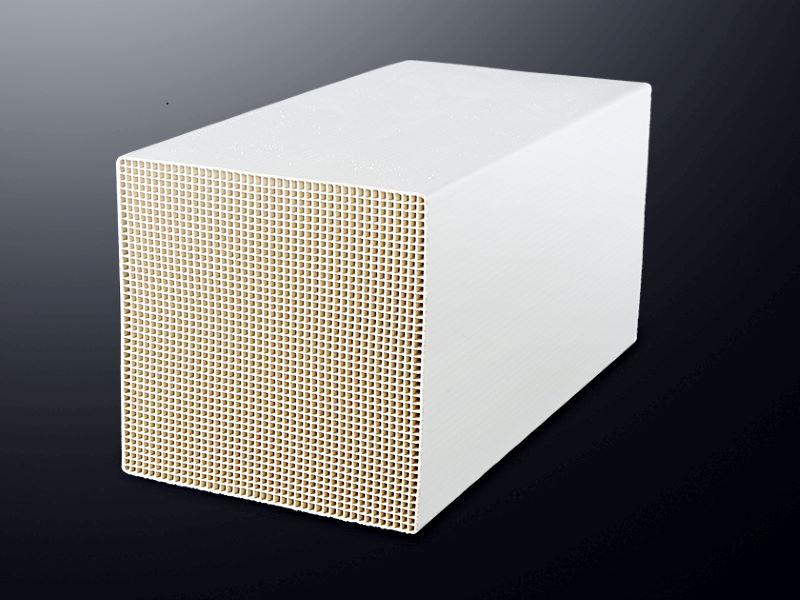
Solution proposed
Our company has developed an innovative solution for drying industrial ceramics before firing, using radio frequencies or microwaves, coupled with steam.
This allows for the precise control of the drying temperature and uniformity:
- Processing time under 20 mn
- Residual humidity below 2%
- 0% reject rate
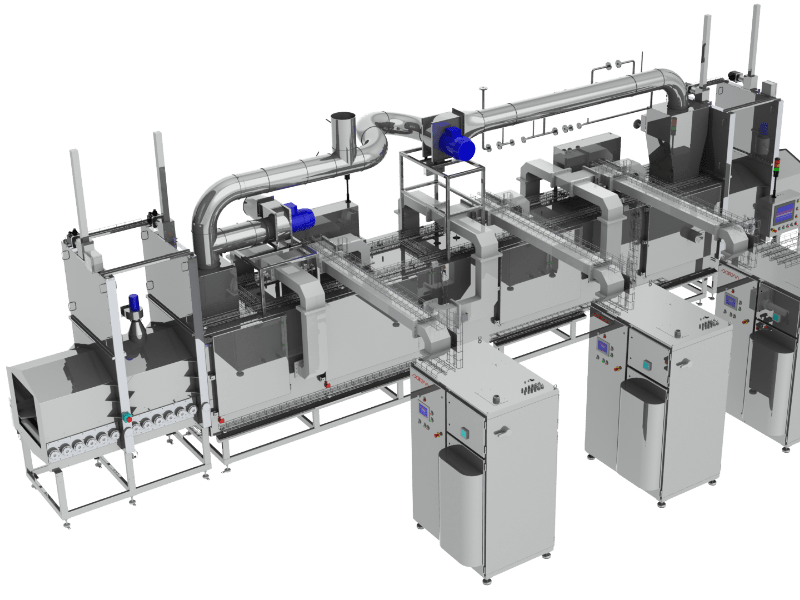
Key benefits
By combining radio frequency with a flow of hot air saturated with humidity, this solution makes it possible to reduce the humidity of the parts being treated from 40% to less than 2% in less than 20 minutes, while also eliminating the risk of deformation or cracking.
Our expertise in the choice of frequencies allows for the selective evaporation of water without heating the material making up the parts.
Contact us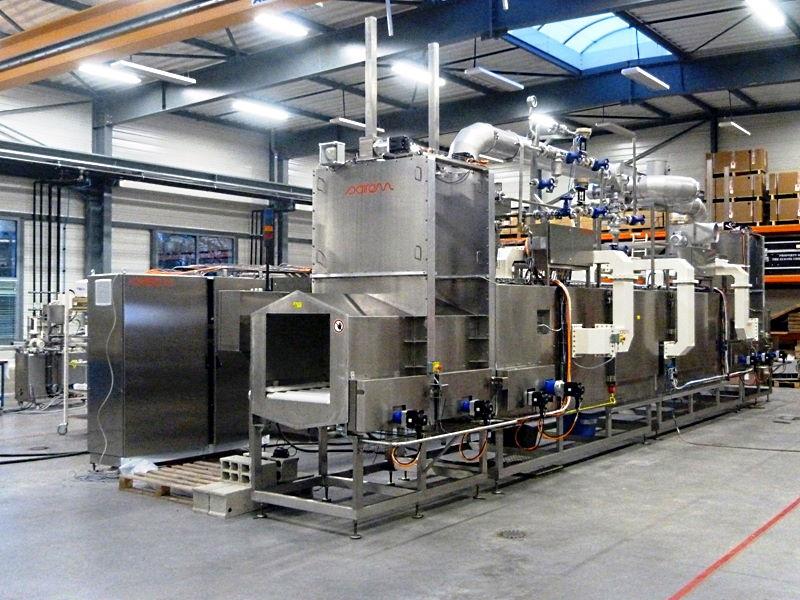